Elevate Your Operations in Packaging: With our Comprehensive Cheat Sheet for Digitalized Performance Management | Tracking & Tracing | Quality Management | Business Connectivity
Implementing digitalization in FMCG industries can indeed be a complex process, and many companies may struggle with knowing where to start, what steps to take, and how to successfully navigate the entire journey. One common challenge is the lack of clarity on what digitalization entails and how it aligns with the company's goals. It's essential to have a clear understanding of the desired outcomes and benefits that digitalization can bring to the processes and overall business.
Manufacturers may have numerous areas that could benefit from digitalization, such as production, inventory management, quality control, packaging, or supply chain. Prioritizing which areas to tackle first requires a comprehensive evaluation of existing pain points, operational inefficiencies, and areas with the most significant potential for improvement. With a plethora of digital tools and technologies available today, selecting the most suitable ones for specific manufacturing needs can again be overwhelming.
To simplify the digitalization journey and assist FMCG companies in overcoming these challenges, we have curated a comprehensive and user-friendly reference guide for digitalization in packaging section. This cheat sheet serves as a reliable resource, ensuring that manufacturing organizations are well-informed about the essential elements and best practices necessary for a successful digital transformation.
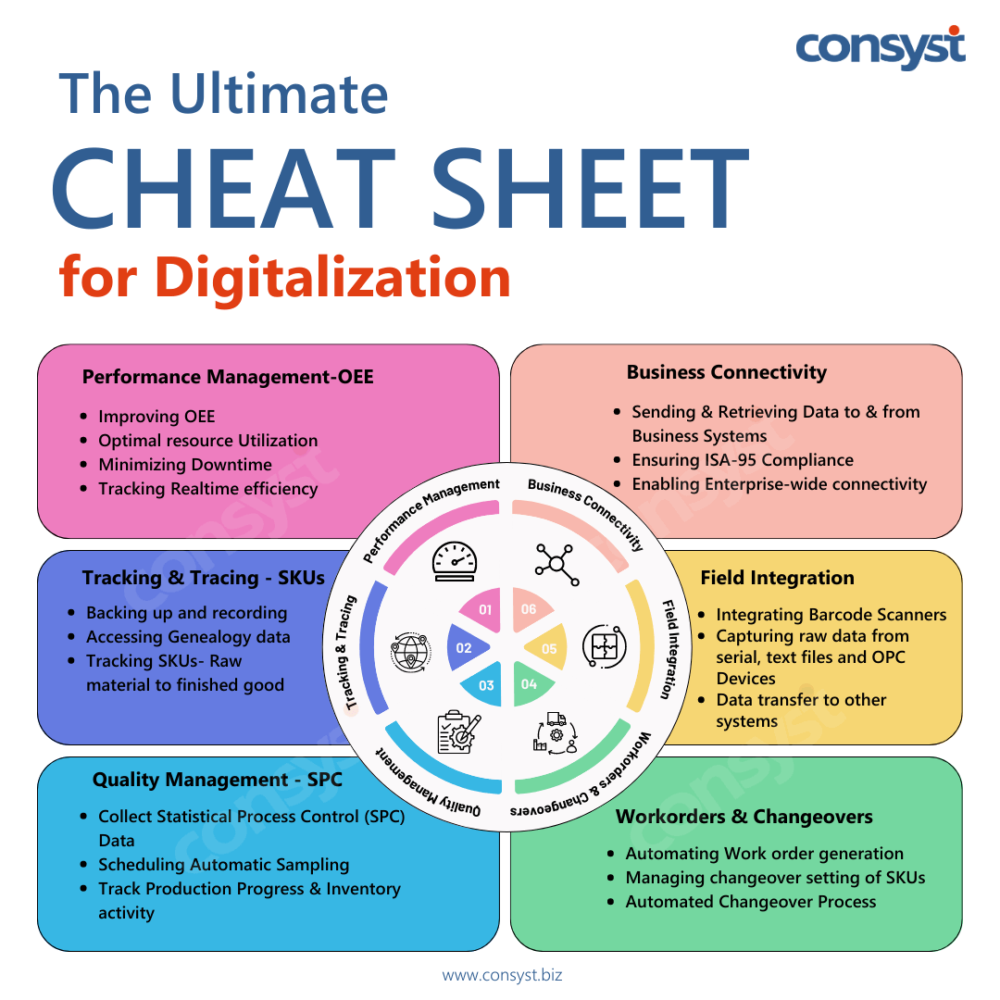
-
Performance Management- OEE
Performance management in manufacturing digitalization focuses on enhancing overall equipment effectiveness (OEE), optimizing resource utilization, identifying performance gaps, minimizing downtime, and tracking real-time efficiency. Performance Management serves as a crucial metric for measuring and enhancing operational efficiency, which directly contributes to increased productivity, cost savings, and improved competitiveness in the packaging section.
By implementing the following strategies, manufacturers can improve their performance:
- Adopting digital solutions specifically designed for monitoring and measuring OEE metrics in real-time can provide insights into line availability, performance, and quality. Real-time data visualization and analytics help identify areas of improvement and enable proactive decision-making.
- Leverage digital solutions to optimize the allocation and utilization of resources, such as labor, materials, and lines. Use advanced planning and scheduling module to minimize idle time and maximize productivity.
- Implement proactive maintenance strategies by utilizing condition monitoring and predictive analytics to minimize downtime. Use data-driven insights to identify potential equipment failures and schedule maintenance activities before failures occur.
- Employing real-time monitoring systems to track production efficiency can help identify bottlenecks or system inefficiencies. Utilizing digital dashboards and key performance indicators (KPIs) to provide actionable insights can help foster a culture of continuous improvement.
-
Tracking & Tracing SKUs
Effective tracking and tracing in production/ packaging lines and products play a vital role in maintaining product quality, ensuring supply chain transparency, meeting regulatory requirements, preventing counterfeiting, facilitating recalls, and driving continuous improvement.
- Backing up and Recording data using digital systems can help manufacturers ensure the integrity and preservation of critical information. Digital systems provide a secure and reliable means of storing data, protecting it from loss or damage due to hardware failures, system crashes, or other unforeseen events.
- Enabling an Audit Trail can allow manufacturers to trace and analyze the complete packing history of a product, including its lines, schedules and associated data. In the event of audits or investigations, manufacturers can provide accurate and detailed records, facilitating compliance with regulations and quality standards.
- Tracking SKUs from processed materials to Finished Goods using digital tracking systems, such as barcode or RFID technology can help manufacturers gain an end-to-end visibility into movement of raw materials, components or finished goods as they move through the production process, ensuring better control and management of inventory.
-
Quality Management- SPC
Manufacturing digitalization allows for greater control and standardization of processes, leading to consistent product quality. By implementing quality management systems, manufacturers can define and enforce quality standards, monitor key quality parameters, and ensure adherence to specifications. This consistency enhances customer satisfaction, builds trust in the brand, and reduces the risk of defects or non-compliant products.
- Collection of SPC (Statistical Process Control) Data through automated data collection systems can help gather real-time data on critical quality parameters. Statistical Process Control (SPC) techniques by collecting data over time and applying statistical methods can help manufacturers analyze process variability and identify patterns or trends that may impact product quality.
- Scheduling Automatic Sampling by integrating sensors and data collection devices can ensure timely and accurate collection of samples for quality testing and analysis.
- Track Production Progress & Inventory Activity in real-time. Integrate with inventory management systems to ensure accurate inventory tracking and reduce waste or stockouts.
-
Workorders and Changeover functions
Workorders are digitally generated directives that provide detailed instructions to operators about the products to be packaged, quantities, packaging specifications, and production timelines. This function also plays a pivotal role in managing changeovers, which involve switching production from one product to another. Through automated changeover processes, downtime is minimized, and setup times are reduced, allowing for quicker transitions between different product runs and optimizing overall production efficiency.
- Digitalized Workorder Generation automates the creation of workorders, eliminating the need for manual paperwork. This ensures accurate and up-to-date instructions for operators, reducing the risk of errors and rework.
- Automated Changeover Processes enables automated changeovers, allowing packaging lines to swiftly switch between different products without significant downtime. This enhances production flexibility and responsiveness to changing market demands.
- Predefined Parameters stores and manages changeover settings for each product, eliminating the need for manual adjustments during setup. This standardized approach reduces changeover time and minimizes the chance of errors.
-
Field Integration
Field integration refers to the process of seamlessly integrating various data sources and devices on the shop floor. This integration plays a crucial role in harnessing real-time data, improving operational efficiency, and enabling data-driven decision-making.
- Integrating Barcode scanners can be an essential tool as they help in capturing data related to product identification, inventory management, and tracking. By integrating barcode scanners into manufacturing processes, businesses can automate data capture, nullify duplication, minimize manual entries, errors, and improve overall efficiency.
- Manufacturing processes generate vast amounts of data from various sources, including equipment, sensors, machines, and production lines. Field integration involves capturing this raw data in real-time from sources such as serial connections, text files, or OPC devices.
-
Business Connectivity
Manufacturing digitalization involves establishing robust connectivity between the shop floor and business systems.
- Compliance with ISA-95 ensures interoperability, data consistency, and standardized communication between various systems. Manufacturers should strive to adhere to ISA-95 guidelines when implementing digitalization initiatives to ensure seamless integration, reduce integration complexities, and facilitate data exchange between business and control systems.
- By enabling an enterprise-wide connectivity, organizations can achieve end-to-end visibility, data sharing, and collaboration across various functional areas, leading to improved operational efficiency, informed decision-making, and enhanced customer satisfaction.
How can CONSYST help?
To know more about suitable Digitalization solutions for your manufacturing industry, contact our experts at solutions@consyst.biz